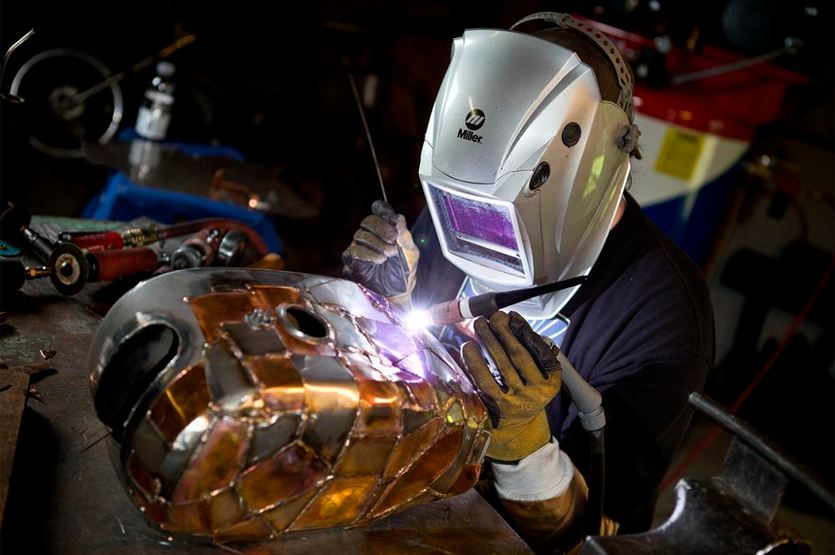
MIG welding is often considered an easy process to learn when it comes to welding. In some regards that may be true, but MIG welding has many subtleties that separate the elite welders from the wannabes. In this article, we are going to go over four things you can practice to improve your MIG welding.
1) Always clean you Material Before Welding.
Clean material is essential when using a gas shielded process. There aren’t any fluxes to clean out the impurities and scale in carbon steel. If you fail to buff your workpiece to clean white metal you are going to risk porosity and pre-mature weld failure.
2) Always Maintain a Consistent Stick-out.
For those who don’t know, stickout is the distance between the conductor tube and the end of the wire. The stickout should be right around ⅜”. An inconsistent stickout is one of the most common errors we see among new welders and it causes irregularities in your weld bead. When the stickout becomes too long, you will hear sputtering in the weld pool.
3) Know your work angles in relation to your position.
Work angle is the angle of your torch in relation to your weld. Most people like to include a 12-15 degree angle while they are welding with the MIG process. Once you start getting past 15 degrees, you may start to experience porosity and excessive spatter in your welds. However, that is in the flat (1G) position. If you are welding out of position the rules just changed. For instance, if you are welding vertical up, you may need to reduce that angle slightly, drop your amperage 10-15% and incorporate a weave technique. This is because you are fighting gravity and special measures must be taken.
4) Know whether to push or pull.
This is going to cause some controversy. At the end of the day (if you are a professional welder) you will weld based on what the WPS tells you to do. However, if you are a home fabricator or weekend warrior you don’t have a WPS dictating your parameters and techniques. The general rule is, “If there’s slag you drag and if there gas you push”. MIG (or GMAW) is a gas process, so unless otherwise stated it is safe to incorporate a 12-15 degree push angle.
The final piece to the puzzle is to PRACTICE, PRACTICE, PRACTICE! While you are practicing you will begin to notice how you move changes the appearance of the puddle and final weld. You’ll notice travel speed will effect the hieght and width of the bead. You can stitch or make a continuous “cursive e” to help give a stacked dimes look.Once you find what you’re comfortable with keep with it until you can’t mess it up and then practice some more!
For more information on MIG welding techniques or help with your own welds, join the Everlast forum or Facebook group.